Manufacturers with an adequate QC solution should resist the temptation to bolt on a separate Document Management System because native integrations offer many benefits.
It runs counter to our instincts and culture to separate the three aspects of quality management – Quality Control, QESH and Document Management (DM) – because Quality Intelligence describes the state of affairs condition where these three inter-operate and become one.
AlisQI is a Quality Management System (QMS) that can bring all three aspects together. Although such a three-in-one architecture is optimal, it is far from being the norm: much of the quality software on the market only ‘does’ QESH, or QESH in combination with DM. Platforms that take a 360° approach to quality management are few and far between.
Why are QC, QESH and DM separated anyway?
We suspect the reasons for this are historical. Manufacturers have been doing Quality Control for longer than quality management, and so the starting point is usually to implement a QC solution, most commonly through a Laboratory Information Management Systems or LIMS. But Document Management and QESH are still run from Excel spreadsheets.
What to do? At first sight, the easiest and most cost-effective remedy is to get licenses for a DM and QESH tool and integrate this into our day-to-day processes. There are many vendors out there offering Document Management and QESH solutions to complement your QMS – and fill a gap in the market.
We said ‘complement’, not complete.
However efficient these tools might be, they are still short-changing manufacturers because they take a limited – and limiting – view of quality management. In the AlisQI conception of QM, all aspects should work together, inter-permeate, for a smarter, omnipresent view of quality.
An integrated QMS, here’s what you can expect
There are obvious organizational benefits to an integrated, one-stop-shop solution. Overall licensing costs will be lower. System administrators manage just one system; end-users work within one UI.
Omnipresence is a non-starter if there are barriers to accessibility, which is why user-friendliness is such an important component of Quality Intelligence. A system that connects the dots natively (and not through integrations, however ‘seamless’) will be more intuitive and approachable and will therefore be adopted more widely.
Over the years you may have got used to jumping from Excel to Module A to Google Docs to Module B and do it very rapidly – but the factory floor is no place for complicated workarounds.
You could argue that these operational advantages are just as important as the functional benefits because Quality Intelligence should mean that everyone is working smarter.
The AlisQI platform was conceived to offer the advantages of integration out of the box. In our QMS, Quality Control and QESH forms link directly to the relevant documents in the internal Document Management System. The traffic goes both ways: process flow charts in the DMS link directly to QC and QESH forms. Actions and events for QC, QESH and DMS are grouped on one integrated action list, one integrated internal calendar. Your KPI dashboards show details from QC, QESH and DMS.
Be thorough and pragmatic in the selection process
Delamine, a medium-sized Dutch manufacturer, owned partly by chemicals giant Akzo Nobel, understood the advantages of an integrated QMS very well. A leading producer of ethyleneamines, the business had put its Quality Control on a sound footing by implementing a LIMS tool. However, management recognized that to reach quality maturity, and prepare for the technologies of tomorrow, it needed every aspect of quality management to be smart and integrated.
The LIMS module came from AlisQI and the manufacturer was 100% satisfied with it. But that is (and was) beside the point. What is so instructive is that the Quality Leader tasked with the job of taking QM to the next level was told explicitly that the positive experience with the AlisQI Quality Control/LIMS module could not play a role in the selection of an integrated system. This was absolutely the right approach: the success of an integrated system cannot depend on the effectiveness of just one component.
You will forgive us if we add that, in the end, AlisQI was selected because its QMS as an integrated whole satisfied the manufacturer’s criteria.
We should add in conclusion that AlisQI puts its money where its mouth is – that is to say, our concept of accessibility and integration is reflected in our business model, which licenses per site, not per user.
We do not tax participation but encourage it in every way we can – and how we implement the quality manual in AlisQI is part of that.
In our next and final blog in this series on Document Management, we will look in more detail at how AlisQI makes your manual more approachable and how its integrations with QC and QESH can drive overall quality in your factory.
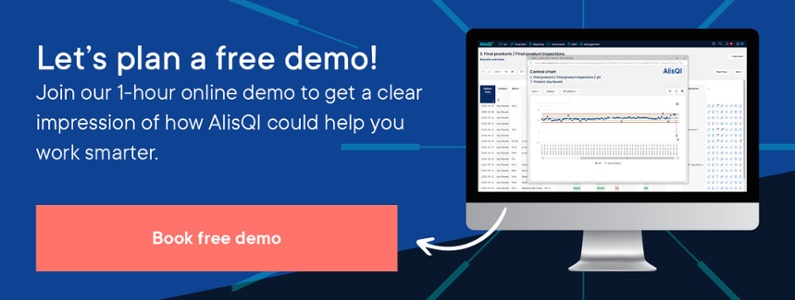
