The Five times why problem-solving method is a straightforward methodology that explores the underlying cause-and-effect of particular problems. The primary goal is to determine the root cause of a defect or a problem by successively asking the question “Why?”.
In this article, consulting firm Herrmann illustrates the Five whys method with a practical example.
Background:
One of our clients is a sheet metal manufacturer. Among other things, the company produces housings for various applications, e.g. for so-called information columns. These columns are installed in locations all over the Netherlands. One day, the company receives a complaint. The gas spring inside the columns is leaking oil, which is causing malfunctions. The damage is substantial. More than one hundred of these columns have been installed throughout the Netherlands. The total damage exceeds €150,000. What went wrong here?
One of Herrmann’s consultants took the initiative to look into the matter. They used the “Five whys” method:
1. Why did it go wrong? It went wrong because the design drawing had not been finished before it was sent to the production department.
2. Why had the design not been finished yet? The design was not finished because the client had not yet decided what brand and type of gas spring it wanted to use.
3. Why was the design sent to the production department prematurely? Time was of the essence. Unfortunately, that is often the case with these types of projects. You have to be fast if you want to compete. The sales department had made a promise to the client regarding the delivery time.
4. Did the people in the production department know the design was not finished yet? Yes. Finished design drawings are stamped to indicate they are ready for release. This particular design had not been stamped yet.
5. Why did things go wrong anyway? It is not uncommon for production to begin before a design has been finalized. There is no hard stop in place to halt production if a design has not been stamped yet. It is unclear who exactly is responsible for uncovering and sharing the missing information.
These answers allowed us to draw up a few key questions that we presented to the management team:
If speed is of the essence in order to bring in new projects, is it a good idea to be able to send non-finalized design drawings into production?
If so:
- How can we indicate what elements are missing? Who is responsible for this?
- How do we make sure the production department receives the missing information when it becomes available?
If not:
- How can we prevent this from happening?
We all make mistakes and some mistakes are unavoidable. You should try to learn from your mistakes, though. The “Five whys” is an effective method that pushes you to uncover the root cause of why something went wrong. It is worth noting that nine times out of ten, mistakes are made because people do not know who is responsible for what. Making clear agreements with each other and honoring these agreements helps you get your quality under control. Use that to your advantage.
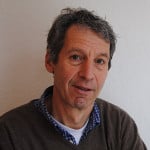