Actively trying to avoid mistakes – and the resulting costs – is absolutely worth your while. In this blog, consulting Herrmann shares a practical example of how concrete manufacturer De Molen* managed to save €130,000 in failure costs with Herrmann’s assistance.
Background
Concrete manufacturer De Molen* produces concrete wells, sewer pipes and drinking water pipelines. The company employs around 130 people. To increase the organization’s profitability, the directors try to lower their costs without compromising the quality of their products and services.
The costs of quality
The “costs of quality” are all the costs of maintaining a certain level of quality, plus the costs of failure. These costs can easily make up 15-20% of the total revenue and can be broken down into:
- Prevention costs: the total costs of preventing problems. Think of performing preventative maintenance on production assets.
- Assessment costs: the total costs of assessing quality. Think of certification costs.
- Costs of failure: the total costs related to quality issues. Think of claims, waste and the costs of repairing rejected products. This money is basically wasted.
These costs of quality are generally not booked as such and are therefore “hidden.”
The approach
The plan
In close collaboration with Herrmann, a plan was devised to significantly reduce the costs of quality. This plan was presented to the MT, with an emphasis on the positive intentions.
How to identify the costs of quality?
To begin with, conversations with stakeholders were conducted and an estimate of the costs of quality was made. With some assistance from the controller, De Molen’s total costs of quality were estimated to be €2,100,000 per year. Breaking down these costs brought some significant differences to light. Reason enough to take a closer look at the production process for the concrete wells.
Square wells
Wells are produced in a variety of sizes and the connection points (holes) are placed in accordance with the client’s specifications. This means almost all wells are unique and made to measure. During production, a mold is made based on a design drawing provided by the work planner.
Identifying the cause
How is it possible that so much waste was created and so much needed to be repaired during the production of the wells? Herrmann worked together with the foreman and the work planner to analyze a number of recent incidents. By asking the right follow-up questions, it became clear that many problems were caused by changes made to orders that had already gone into production. These changes resulted in multiple versions of a design circulating on the work floor, which in turn lead to production errors.
Minor changes, major impact
With some assistance from Herrmann, the foreman and the work planner quickly came up with a solution. The work planner would begin taking back outdated designs and it was agreed to carefully discuss any changes that were made in the future. The impact of these changes was monitored for three months and turned out to be significant. With a few simply measures, a total annual savings of €130,000 was realized on the production of square wells alone!
Conclusion
Making mistakes is practically unavoidable. However, you can do to avoid making the same mistakes over and over again. By critically examining your costs of failure, listening to the people on the work floor and, above all, identifying the root cause of issues, you can achieve a whole lot with very little.
* The names of the organizations are deliberately fictitious
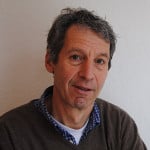