The term ‘omnipresence’ is not appealing and sounds like something out of a bad sci-fi movie, complete with an eerie 70s soundtrack. Nevertheless, it has stuck as a marketing term because it describes very well what you want to achieve, particularly when it comes to quality management.
There is nothing futuristic about omnipresence. For a manufacturer, it is no more complicated than that everyone in the business should be involved with quality, and have the ability to do so.
If this sounds like common sense to you, you’d be right. Yet, omnipresence as we have defined it here is not nearly as common as you might expect. The reputation of a manufacturer stands or falls with the quality of its products, and whether it can turn a profit depends on how cheaply quality can be achieved and maintained. The effectiveness of quality management, in other words.
So you’d expect quality to matter to the boardroom as well as the shop floor – to be omnipresent. But oddly enough, that is not often the case: quality as an operational function is often overlooked and neglected.
Part of the blame must lie with quality cadres who can take a (too) narrowly technical view of their job, and don’t always get out of their comfort zone enough to advertise the strategic role that quality should play in a manufacturing business.
This organizational dissonance always goes hand in hand with frustrating (and unnecessary) technical limitations that affect Process and Systems. For omnipresence to take hold, these have to be integrated.
From fragmentation to integration: The core activities
Just as omnipresence breaks down barriers between departments, it also blurs the distinction between the three ‘building blocks’ of quality management: Quality Control, Document Management, and QESH.
Omnipresence gives manufacturing companies an integrated, 360° experience of all these core activities. The integration needs to be all of a piece, and not an integration after the event – usually, a reporting tool or Document Management module bolted on to an existing Quality Control solution.
Over the years you may have got very good at navigating between Quality Control, Document Management, and QESH but you are still wasting precious time, as well as fatally excluding everyone else from the process. These juggling acts do not deliver omnipresence.
You want your QC and QESH forms to link directly to the relevant documents in your internal Document Management System (DMS). Process flow charts in that DMS are linked directly to QC and QESH forms. Actions and events for QC, QESH, and DMS are grouped on one integrated action list, one integrated internal calendar. Your KPI dashboards show details from QC, QESH, and DMS.
All the results of all your activities are always up-to-date in place, for everyone to see and use.
From fragmentation to integration: Process and Systems
Every Quality professional will have encountered the following state of affairs at some point in his or her career.
You are hampered by legacy systems, making quality data and documentation difficult to access and update. You are struggling with a fragmented and out-of-date corporate structure, with each department running its own show, operating different systems and procedures. There are too many hoops to jump through, even for routine quality processes. Endless calls and emails are needed to plug the gaps, but the inevitable miscommunications only lead to more problems.
It is not agile.
The view from the top is no clearer than the day-to-day experience of quality teams, and so there is no organization-wide insight into quality, and no viable quality planning as a result. Finally, a manufacturer with poor insight into its own practices can have little control over the integrity of its supply chain.
So what does omnipresence look like?
Data scattered on many megabytes of Excel spreadsheets are now stored in one central place. Your shop floor in Laos is looking at the same real-time and up-to-date information as your sales representative in Lausanne.
The data and the meaningful analysis of that data are accessible to everyone. No more out-of-date manuals. No more worrying over audits.
For any question about a complaint, you have the answer to hand. Factory shifts are looking at the same Quality data, so no more mishaps and confusion during handover.
Routine quality meetings are sped up because the quality indicators and actions points are available to all participants on a system dashboard.
This is not sci-fi, but common sense. But it is the kind of common sense that can only be established with a clear impulse from the top. Omnipresence begins in the boardroom.
To find about more the importance of omnipresence in Quality Management, download our whitepaper “How to prepare for Quality Intelligence“.
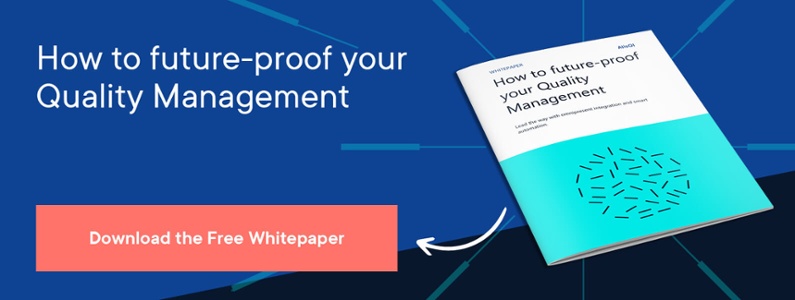
How to prepare for Quality Intelligence?
Learn how to self-assess to what extent you are ready for Quality Intelligence, and leverage tomorrow’s possibilities.
