Autoliv masters the quality of their life-saving products
Customer case study: Autoliv Inc.
Quality Control & SPC tool for Autoliv
Autoliv, the world market leader in seat belts and airbags needed to improve its production quality control and statistical process control.
Over the past years, Autoliv selected and implemented AlisQI as a “Production LIMS” on 10+ production plants around the globe.
The results: fewer errors, direct feedback, and live test data available for everyone. This not only saves a lot of time, but it is also a basis for continuous improvement!
Before AlisQI my team had to compare the measurements manually with specifications on a separate sheet.
Laboratory Manager Autoliv Airbags International
Craig Lees
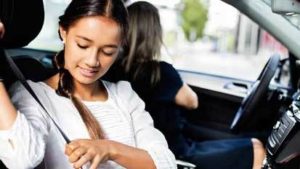
Around the globe
Autoliv’s life-saving products require thorough quality control procedures and systems. To that end, Autoliv was looking for a Laboratory Information Management System (LIMS) with just the functionality you need in a factory environment.
On the other hand, Autoliv wanted more support for real-time process control and reporting, than you would find in an ordinary LIMS.
Autoliv implemented AlisQI as productions LIMS around the globe.
Laboratory Team Leader Autoliv Inc.
Craig Lees

Administrative procedure was error-prone
Part of the Autoliv airbags are produced in the Congleton factory in the UK, where Craig Lees works as a Laboratory Team Leader.
“Our operators perform many quality tests”, he explained. “They cut out samples, and test the thickness of the nylon, the strength, the elasticity, and the warp and weft pattern. The measurements are done in two laboratories, located directly beside the production line. The operators enter the data into the computer. If the results are good, the corresponding batch of airbags is released and shipped to other Autoliv sites for further assembly and finally to car manufacturers, which are customers of Autoliv.”
Before Autoliv started to use AlisQI they faced several problems. “The operators used to fill in forms in our Product Lifecycle Management system”, Craig Lees continues.”However, they got no warning when they entered deviating data. Secondly, to check if an airbag passed or failed the test, they had to compare the measurements manually with specifications on a separate sheet.”
So the whole administrative procedure was not only error-prone, but it also took a lot of time.”
“Initial thoughts were that finding new software did not have high priority, since the current test method, although time-consuming, did work. In such a case one can easily become blind for improvement opportunities. Especially in hectic periods, people are inclined to go on as they did before.”
“Later, the IT department tried to develop made-to-measure software to overcome the problems. Their solution was based on Excel datasheets and an Access database, but this was no success.”
“The breakthrough came during a conference call with one of our sister factories in Holland. They were using AlisQI to record the dimensions of the seat belts they produce.”
“When we heard that, we thought: if that works so well, why not use that LIMS here with additional requirements, as a test managing system. After all, that is what AlisQI is designed to do.”

3 easy steps to convince everyone that you need a QMS
On this page, you’ll find all the necessary resources to build a strong business case
for Quality Management and convince stakeholders that you need a QMS.
Before AlisQI, my lab technicians had to compare the measurements manually with specifications on a separate sheet.
Laboratory Team Leader Autoliv Inc.
Craig Lees

Pilot was successful
Autoliv strives to keep its ICT portfolio as small as possible.
“We have a ‘one product, one process’ philosophy. Therefore, we knew that we would get permission easily to invest in AlisQI, since many Autoliv factories were already using this software.”
AlisQI Co-founder and CEO, Gerben de Haan came over to England for a demo.
“This was free of charge. The software runs on a server in Holland, to which we connect via a secure connection. We do not have to bother about software updates. We became enthusiastic and started a pilot with the system. We entered real specification data, and our operators started to feed it with test results.”
“The pilot was successful. After some changes and editing to suit our needs, the software was ready to roll out completely. It took us only three months, and our operators became used to working with AlisQI very quickly. In fact, their work has become much easier, since the system guides them through the whole test procedure.”
“On the screen, they see a 2D drawing of an airbag, and all the points from which samples should be taken. And when they enter their test results, it is immediately clear if these are OK or not. NOK results are highlighted in red. When a test is complete and the results are OK, a label is printed automatically that includes all the quality information. This saves us additional time.”
The work of lab technicians has become much easier, since the system guides them through the whole test procedure.
Laboratory Team Leader Autoliv Inc.
Craig Lees

New way of working
The new way of working has improved the quality of the test procedure a lot. “The number of incorrect data entered dropped dramatically. The software helps the operators to do it right first time.”
AlisQI not only structuralized the test procedures but the data can also be used for continuous improvement. This might even concern production steps way before the final fabrication of the airbags.
“To that end, the test data is in real-time available to everyone. We added a module for statistical process control. Now we can see which parameters are still capable at any particular moment, or start to drift.”
“Operators at the weaving machines for example can use this, to check if their process contributes to a negative trend. If so, they can adjust it, before a real problem occurs.”
“Having used AlisQI for three years, the database has become filled with millions of data points. The system is however just as fast as it was in the beginning. And it is very flexible as well. As I already told you, the software package is running on a server in the Netherlands.”
“However, we wanted to have our own copy of the test data, among others to satisfy the traceability demands of our customers.”
“Therefore AlisQI built a two-way connection between our IT system and their server. Each day at nine o’clock we receive an update of the test data.”
“In addition, we send specification data back. For example, new test limits, to be used during production batches in the next week.”
Now we can see which parameters are still capable at any moment, or start to drift.
Laboratory Team Leader Autoliv Inc.
Craig Lees
Lean Six Sigma
By building a production history, Autoliv Congleton will gain insight into their production process.
“The process history can be used for continuous improvement with Lean Six Sigma. In addition, test data might be compared between plants, to learn about each other and to find the parameters for best practices.”
“For example, our factory in Canada is implementing AlisQI right now, so we can compare our tests with theirs in the future.”
Another site that implemented AlisQI this year, is the seatbelts factory in Sao Paulo.
“During several consecutive production steps, we take samples of the belts and measure, for example, the strength, the thickness and the elasticity”, says Rodrigo Gonçalves, Process and Product Development Engineer in Autoliv Brazil. “We used to note the results on paper or in spreadsheets. This lengthened the time to find data, and that made it nearly impossible to find the root cause of a problem.”
“To find a correlation between any parameter and a situation, you need a lot of historical information. AlisQI provides this. For more in-depth analyses I can easily export data to Minitab.”
With AlisQI, all the process history can be used for continuous improvement with the SPC Six Sigma toolkit.
Laboratory Team Leader Autoliv Inc.
Craig Lees

About Autoliv
The Swedish-American multi-national company Autoliv is the largest automotive safety supplier, with sales to all major car manufacturers in the world. They produce airbags, seat belts, (intuitive) steering wheels, pedestrian protection.
Each year, they make enough seat belts to cover the distance to the moon, and they produce 150 million airbags in great diversity.
Let's plan a free demo!
We would love to show you how your factory can benefit from using our software, save up to 20% on time and reduce waste by up to 15%! Join our 1-hour online demo to get a clear impression of how AlisQI could help you work smarter.