Our quality has come alive
Customer case study: Berry Global
"How AlisQI transformed Quality Management at Berry Global in just four months"
Key takeaways
- Wendy Beks, Senior Laboratory Technician at Berry Global implemented the Quality Intelligence system AlisQI in just four months, with only 3 days of support from AlisQI
- AlisQI now saves 10 hours a week in data cleansing alone
- All process data, quality data & statistics are now available in one place: in AlisQI
- Everyone has immediate access to all data: operators, lab technicians, and management
- Berry integrated AlisQI with their WinCC SCADA: just 10 lines of code
- Berry integrated AlisQI with their ERP, using QR codes
Everybody is surprised & enthusiastic about the benefits of AlisQI: “I am learning. I am learning from my own processes.”

History
In June 2019, one of the European facilities of Berry Global, a world leader in plastics, packaging and non-woven specialty materials, implemented a modern Quality Management platform.
The plant in question, located in the Netherlands, had been acquired in 2015 by Berry Global as part of its $2.5bn takeover of Avintiv, a specialist in hygiene and personal care products that had only just undergone a corporate rebrand and restructuring itself.
In this whirlwind of events, Quality got left behind. In as far as it was even on the radar of senior management, the initiative and investment necessary to modernize Quality Management were being put off, year after year.
However, the experts on the ground were tenacious in pressing for change. It was them who experienced every day just how urgently Berry needed a technologically advanced solution to integrate and automate its quality processes. Foremost among these advocates for change was Senior Laboratory Technician Wendy Beks.
If you wanted to know something - certain data of a production line - it took an absolute age but now with AlisQI it’s two clicks and you have your graph.
Laboratory Manager Berry Global
Wendy Beks
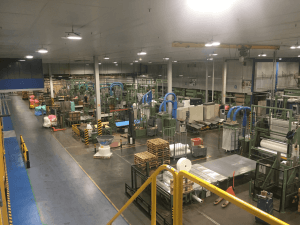
No ERP system has a real Q-module
Beks has come to realize that ERP never delivers effective Quality Management.
“With any ERP system, Quality is tricky,” she says. “I was involved in the development of Oracle as the successor of our own custom-made ERP on an IBM AS/400 computer. You have to put in a whole new quality routing, which means you are effectively starting from scratch. Then we looked at JDEdwards. Same problem. Oracle and JDEdwards don’t have a quality module so it’s up to you to devise everything.”
Because of the lack of real Q-management, many companies invent workarounds and maintain a shadow quality administration in Excel. “Everyone keeps his own books and has his own tips and tricks to make that data meaningful to them. But of course, that’s difficult to share.”
The data difference
This is where AlisQI has been the most transformative: all data is accessible to everyone in one central place. “All over the company, we have cupboards with boxes of files, and computers of course where we keep the folders with our ‘stuff’ …”
Beks starts to import all data going back to 2016. Having all data in one central place saves Beks and her team a lot of time. Before AlisQI, typing errors, improper data entry, and incorrect certificates had to be corrected: “this took us 10 hours a week.”
Producing graphs was a time-consuming and frustrating process. “We couldn’t get downloads from the AS/400 ourselves,” Beks explains. Only one or two people were able to do that, with a lot of effort, but they were not always available. “So you had to copy everything page by page in Excel … If you wanted to know something - certain data of a production line - it took an absolute age but now with AlisQI it’s two clicks and you have your graph.”
Flexible means tailormade
Customization is another transformative functionality in AlisQI.
Beks explains. “You can determine for each user what he or she gets to see. Operators don’t need to see 30 choices. Only their production lines and dashboards.
Team leaders have the authorization to see a lot more yet without the authorization to adjust the results. Because if something is off-spec, you do not want that data changed. And if this inadvertently happens, you have traceability. There is an audit trail for everything, including your spec history, so you can identify exactly when something was changed, and by whom.”
One of the anachronisms of the old system was that it only recognized one specification. “If you changed one spec, the spec was changed for the entire history,” says Beks. “With AlisQI, you just enter the start date of the new spec which means you are comparing like with like: old data with old specs, and recent data with your latest specs. So you don’t suddenly get a whole lot of deviations because you changed just one spec. But that’s precisely what used to happen.”
Poor data equals poor analysis
Beks has come to realize that ERP never delivers effective Quality Management.
Trend analysis required a lot of hard work and patience with the inevitable that Berry had less than adequate insight into the development of quality. “Process engineers spent a long time on specification evaluations,” says Beks. “Someone had to get a year’s worth of data out of the system, this had to go into Excel, the errors had to be weeded out, you put your graph on top of it, and then - finally - you checked this against your spec.”
Beks adds: “But there were no statistics.”
The situation could hardly be more different today with AlisQI instantly retrieving and contextualizing data - not in Excel but on clear and highly intuitive dashboards, customized by Beks.
Adaptable technology
As we mentioned earlier, ERP systems are not made to run Quality Management and with AlisQI, Beks would argue, Berry no longer needs it for this purpose. Quality Management has escaped from the straitjacket of a technological legacy that was both fragmented and rigid.
AlisQI is able to overcome the limitations of existing systems by being extremely flexible and customizable. This Beks discovered during the pilot.
“Together with AlisQI, we designed the analysis scheme for one of our production lines - the tests we needed to include and against which specifications we would benchmark the measurements. The software is highly intuitive: it really takes you by the hand. You watch how it’s done once, and you’re good to go.” Therefore she could implement the other lines herself.
She adds: “Naturally if there’s a question you ping AlisQI an email and they get right back to you.”
The software is highly intuitive: it really takes you by the hand.
Laboratory Manager Berry Global
Wendy Beks
Seeing is believing
Beks has come to realize that ERP never delivers effective Quality Management.
The new QA manager, Kaoutar Bouaoud, ended years of Quality stagnation by saying: “for good ideas, there is always money”. The demo of AlisQI did the rest. Beks: “Kaouter is a Lean Six Sigma Black Belt, so she is all about the numbers and she can tell immediately from graphs and statistics what is going on. So AlisQI is ideal for her.”
For the process engineers who track quality on the ground, create new specifications, and monitor the tests, AlisQI was nothing short of revelatory. “They could get to the graphics, but not nearly as quickly as is the case now. When they saw AlisQI in action, they had that shock of, so it can all be as easy as this?”
“We had a brief look at a few other systems but did not take it any further. When we piloted AlisQI we saw at once what it could do and we knew at once: this is the best.”
Beks and her colleagues wanted a system with the right toolkit of functionalities, yet they soon realized that AlisQI gave them more than that. Its open and adaptable approach gave Berry ownership - without which Quality Intelligence cannot be achieved.

3 easy steps to convince everyone that you need a QMS
On this page, you’ll find all the necessary resources to build a strong business case
for Quality Management and convince stakeholders that you need a QMS.
With AlisQI, data is accessible and transparent, also for our operators who finally have a statistical tool to interpret quality data.
Process engineer Berry Global
Hendrik Reynvaan
Integration with production data
The AlisQI software is so approachable that Berry’s senior electro-engineer, Rini Roijendijk, was able to connect the platform to their Siemens WinCC data acquisition system without any previous experience. This integration with the AlisQI API was crucial because it gave everyone at Berry access to real-time data.
Roijendijk explains: “For every machine, at five-minute intervals, I generate a text file in WinCC with the variables I want to read. A program of just 10 lines of code sends this to AlisQI.”

Involving the factory floor
Another colleague instrumental in the success of AlisQI is process engineer Hendrik Reynvaan who played a key role in introducing the factory floor to the benefits of AlisQI.
“We had real-time data before but it was highly fragmented,” Reynvaan says. “With AlisQI, it is accessible and transparent, also for our operators who finally have a statistical tool to interpret quality data. How is that data distributed? How reliable and accurate is it? You can show your operators and process engineers trends, which gives them a lot more insight into their own data. It’s great.”
Reynvaan organized an awareness meeting where he let the operators loose on AlisQI - to play with the data, explore the possibilities - to give them ownership of the new system.
It is working. “Only today I asked an operator: ‘Do you use AlisQI?’ And he replied: ‘Absolutely. I am learning. I am learning from my own processes’.”
For process engineers and operators, AlisQI has been a real eye-opener. The new culture of insight and growth is boosting quality in every part of the production process - and is giving Reynvaan insights he had not anticipated.
“It’s much easier to observe the differences between production lines,” he explains. “Some give us more problems than others, and always the same kind of problems. We now see that these problems are not really caused by the process itself but by the way we measure it. We have to resolve this because these are crucial quality parameters.”
I am learning. I am learning from my own processes.
Operator Berry Global

Future plans
Customization is another transformative functionality in AlisQI.
Beks and her colleagues have achieved a lot in the four months since AlisQI was implemented. But they are not resting on their laurels.
One of Beks’ near-term goals is to generate all certificates out of AlisQI and use the platform to oversee incoming deliveries.
The Quality team is deciding whether to assign the entire job to AlisQI or to take a shortcut by simply adding the certificate as an appendix to each delivery.
“At the moment, if there is an issue with raw material, to find the certificate you have to go to the lab and find the right folder, the right article number, the relevant delivery, and so on.
“Once we have put this in AlisQI, we’ll be able to go into the system and go, okay, I have this fiber on this line, these are the problems I have with it and AlisQI takes you straight to the appendix. And there you have it: our supplier’s certificate and the data of the tests that we do. So you’d have that information in front of you in two, three clicks.”
Beks and her colleagues have achieved a lot in the four months since AlisQI was implemented. But they are not resting on their laurels.

Spreading the message
The facility in the Netherlands buys and sells materials and products internally from other Berry Global facilities so there would be obvious benefits to working with the same Quality Management solution.
Beks gave colleagues from Berry Fiberweb Berlin a guest log-in to AlisQI, and they got on so well with the system it has been implemented in December 2019.
She sees other opportunities. “For example, we buy raw materials from a Berry plant in the United States.
This is the ‘system’: they take a screenshot of the statistics, paste that into Word and type our data into it. Unsurprisingly, there are often errors in that.They’ve already said, ‘If you find a good system let us know’ because they’re fed up with this.
“We now have this good system,” Beks concludes. “With AlisQI, we could view the quality data of what they deliver to us via the lot number. No more pasting into Word!”
Conclusion
AlisQI has been transformative in no small part due to the tireless efforts of Wendy Beks who had her sights set on the system as long ago as 2014. In the end, she had to wait five years for AlisQI to be implemented.
Management has been richly rewarded with the trust they put in Beks - and they are “incredibly enthusiastic” about AlisQI.
This buzz about Berry’s reinvigorated Quality Management is spreading. Beks shares her experience with visitors, auditors, and Quality colleagues at other Berry facilities who are also noticing a new tone of insightful confidence.
“These are simply best practices,” Beks concludes about her work with AlisQI. “And we have to roll them out everywhere.”
About Berry Global
Berry Global is a Fortune 500 global manufacturer. It is a world leader in plastics, packaging, and non-woven specialty materials. The European facility was acquired by Berry Global as part of its $2.5bn takeover of Avintiv. In the Netherlands, Berry Global produces nonwoven fabrics, for Swiffer, Zwitsal & J Cloths (in the Anglo-Saxon world).
Customer spotlight
Primus Wafer Paper: quick implementation and AlisQI launch before scheduled kick-off
TenCate Grass: digitalization and 86% time savings
Cosun Beet Company: reduced processing time with predictive calculations
Cosun Beet Company: integration using the AlisQI API; a developer’s experience
4 excellent reasons to integrate AlisQI with PowerBI
3 times manufacturers saved time with Certificates of Analysis
7 advantages of Laboratory Quality Control Software
7 tips for stress-free audits & optimal manufacturing performance
Let's plan a free demo!
We would love to show you how your factory can benefit from using our software, save up to 20% on time and reduce waste by up to 15%! Join our 1-hour online demo to get a clear impression of how AlisQI could help you work smarter.