Improved Quality at Bison International
Customer case study: Bison International
Improved quality at Bison International
From a self-developed system consisting of a large number of Excel documents to a single system in which all quality data are electronically recorded. The arrival of AlisQI has boosted Quality Control at Bison International in Goes.
- Before AlisQI, Bison managed a few hundred Excel files
- With AlisQI, all QC data is managed with a single system
- Operator dashboards show trends and corrections
- Integration with ERP assures up-to-date master data
- Roll-out went very smooth
- Bison now has better information to optimize processes
Our process operators can now control production faster and more accurately than before.
QA & ESH Manager
Ben Lebeau
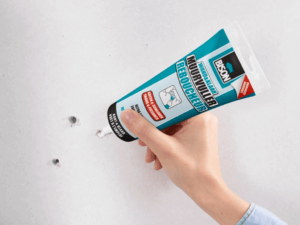
From paper-based to digital
In mid-2012, much of the information transfer within Bison was still a paper shuffling experience. By 2013 everything had gone digital.
The implementation of AlisQI has given quality control at Bison International in Goes a genuine boost, according to QA Manager Ben Lebeau and Analyst Marco Oele.
Operators can now see if the measured values of their tests fall within the specifications at the push of a single button. Copying data by hand is no longer necessary. “This package is much more user friendly,” says Lebeau.
Everything is pre-programmed. Things such as date and batch numbers are automatically prepared following the planning and inserted into AlisQI.
The operator then measures his production values, checks the specifications in the system and will immediately know that everything is fine.
And with a production LIMS like this, everything is safe and secure. The laboratory also has immediate access to the data.
Oele: “In our lab we can place our numbers gathered from the 24 hour check next to the operator’s for the certification. This has greatly reduced the amount of work and improved the quality.”
Our process operators can now control production faster and more accurately than before.
QA & ESH Manager Bison International
Ben Lebeau

Faster & more accurate Quality Management
From its main location in Goes, Bison International develops and produces high quality adhesives, sealants and maintenance products for DIY enthusiasts and professionals.
The company was seeking a production Laboratory Information Management System that would closely connect with a production and quality control environment. They needed a slim package, focused on the operators.
Lebeau: “This package has exactly what we were looking for. It falls right between our old Excel system and the larger, traditional LIMS packages. It works in the cloud, so there are no extra servers, which made it very attractive price wise.”
Bison International has quite a number of different recipes to manage in the production process. With AlisQI, the operators can check if the batch they are working on meets the specifications.
“Thanks to this system we can now steer production faster and far more precisely than previously.”
A production dashboard was added to AlisQI’s standard functionality upon request. Lebeau: “The operator can log on to this, view the screen and enter the product measurements. This module didn’t come as standard with AlisQI and has been configured specifically for us.”
Oele: “AlisQI co-invested in this, as they could immediately see the benefit of such a dashboard for other AlisQI users. Everyone profits, lifting the LIMS to a higher level.”
This saves everyone a lot of work and the quality has improved.
QA & ESH Manager Bison International
Ben Lebeau


3 easy steps to convince everyone that you need a QMS
On this page, you’ll find all the necessary resources to build a strong business case
for Quality Management and convince stakeholders that you need a QMS.
Implementation and cooperation
Implementation started after the summer of 2012. The dual running of the system began in October. Various teams migrated the data and the product list onto the system. The final details were implemented together with AlisQI.
Oele: “AlisQI supported us when transferring the old Excel documents and they provided the training element.”
“They also added a handy small window for rapid access to adjusting the production, for example by adding extra solvent. Collaborating with AlisQI was a satisfactory, accessible and flexible experience.”
The system was rolled out to the QA-QC departments in November. How was it received on the work floor?
Lebeau: “All operators had been trained by us, given a user name and password for the system. I got a few phone calls in the first week, but overall things went really smoothly.”
The package immediately proved its additional value. “The biggest benefit comes from measuring and recording quality parameters in the system.”
“You can now see the latest data, which we couldn’t before, and you can follow the operators better via direct non-conformity reports.”
“We now get a lot more information from the data, which makes us able to optimize the processes.”
Collaborating with AlisQI was a satisfactory, accessible, and flexible experience.
QA & ESH Manager Bison International
Ben Lebeau

About Bison International
Whoever says adhesive, says Bison.
Whoever thinks Bison, thinks adhesive.
The Bison brand is part of Bolton Adhesives. Bolton Adhesives represents the adhesives division of the Bolton Group and has four prominent brands: Bison, UHU, Griffon and Air Max.
Bolton Adhesives products offer the best solutions for bonding or sealing paper and cardboard, leather, fabric and wood, as well as for joining metal and plastic. At home, in the office, at school, for DIY projects as well as professional jobs. The Company’s distribution channels consist of supermarkets, office supply stores, do-it-yourself stores and the professional market. Bolton Adhesives employs approximately 700 employees.
Let's plan a free demo!
We would love to show you how your factory can benefit from using our software, save up to 20% on time and reduce waste by up to 15%! Join our 1-hour online demo to get a clear impression of how AlisQI could help you work smarter.