AlisQI for Diversey
- All QA/QC/QESH data in a single system
- Efficiency boost for Quality Control laboratory
- Automated Certificate of Analysis saves a lot of time
- Drastically improved QESH and CAPA management
This is what we love: all data in one place … we should have this system everywhere, we should have it worldwide.
European Operational Excellence Leader Diversey

The challenge
Before 2016, the Dutch factory used Google Docs and Google Sheets for its Quality Management, but this proved unsustainable as Site Manager Ruud Nijlant explains. “The big disadvantage of Google Docs is: there is no history. If you delete anything or create a new version of a Google Doc or Sheet, that’s it. You cannot see trends and of course you have duplicate data in different places. We had no overview of what we were doing, to be honest.”
The factory carried out a beauty parade of several Quality Management Systems, with AlisQI coming out on top. “We preferred AlisQI for many reasons,” says Nijlant. “First of all, we wanted to have all the data in one place: for the factory, the offices and the Quality Laboratory. We had too much data scattered in too many places.”
The fragmentation of quality data made the issuance of Certificate of Analysis documents increasingly time-consuming. Complaint handling was also challenging because the data overview to support a good workflow model just wasn’t there.
“With the introduction of AlisQI we have everything in one place,” says Nijlant. “This saves us a lot of time and money, and it is absolutely clear who did what, when, and where. “We have been able to create a standard report on complaints and internal deviations.”
AlisQI was selected for its user-friendliness and the flexibility of its Platform. This made it easy to implement and adapt to the specific requirements of the Dutch plant.
We wanted to have all the data in one place, both for the factory and for the quality laboratory.
Site Manager Diversey
Ruud Nijlant


3 easy steps to convince everyone that you need a QMS
On this page, you’ll find all the necessary resources to build a strong business case
for Quality Management and convince stakeholders that you need a QMS.
Grip on complaints, actions and deviations
Prior to the implementation of the AlisQI Quality Management System, the management of actions and deviations was not transparent. Actions were reported of course, and an email correspondence resulted – but this was never systematic. “The person with the closest interest in the action had no idea where it was, regardless of whether it had been solved,” Nijlant says. “So he’d think: ‘I reported this, but nothing has been done about it’.”
AlisQI has resolved this issue. “Not a silver bullet for every issue, but at least we are now addressing everything. And by ‘we’ I mean everyone in the organization: office and factory, that’s the beauty of it.”
Nijlant continues: “Because of AlisQI, it is now just completely traceable who picks up what, when, and where. Which is exactly what we were looking for.”
The AlisQI platform has not just improved internal processes. “We used to do everything manually by email,” Nijlant says. “We had Excel lists and then we’d send the buyer a report, where we all had to enclose documents as an attachment. Many attachments!”
With AlisQI, this data is in one place, accessible to all. “So you can see very easily what the outstanding points are, and the status of every particular finish.”
This information is collected in standard reports for the weekly and monthly Quality meetings. The plant’s Quality Manager receives a breakdown of the outstanding complaints, the complaints processed and internal deviations. The automated reporting through AlisQI makes it much easier to prepare for these routine meetings.
Nijlant comments: “Many reports now run automatically because a template has been created for them. This way we can now also carry out our analyses much easier on the First Time Right performance.”
It is now just completely traceable who picks up what, when and where. This is exactly what we were looking for.
Site Manager Diversey
Ruud Nijlant
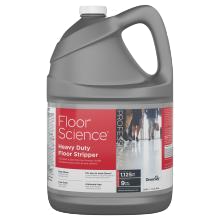
An efficient, sustainable process
The transparency achieved with AlisQI is simplifying the audit process. “Alis gives us the open actions in a clear overview,” Nijlant explains. “We can easily see if there are repetitive patterns in our data collections.”
During a recent audit, the Quality Team was asked if they could now prove that problems had been adequately resolved. Answer: yes.
Nijlant goes on to explain. “In the past, things were all loose ends, nobody was looking at anything systematically, but now carry out a much deeper trend analysis to make the effectiveness of the measures transparent, and it saves a lot of time for QA and QC.”
“We now apply SPC at the shop floor, which means we have significantly reduced the paper shop. In fact, we are working towards a completely paperless factory.
“Our QA / QC processes are running much better. Everything is traceable – we can track whether the processes are running correctly or not.
“At the Quality Laboratory, that saves me time and a lot of frustration with my team, and I’m talking about ½ FTE for the lab alone.
“While I do not lose people because of these standard reports, a lot of people in my team have gained a few hours a week – time freed up to carry out analyses, which contribute to better efficiency.
“AlisQI is a great enabler. The platform is helping me to get my business running efficiently, and we now have a much more sustainable process.
“We can now really do proper analyses. For instance: how often does it happen that certain raw materials or formulations were not First Time Right? We were not able to run these evaluations with our paper and spreadsheet-based methods.”
Audits are now much easier. We now have a clear overview of all open actions.
Site Manager Diversey
Ruud Nijlant

An enthusiastic Operational Excellence Leader
When Diversey’s European Operational Excellence Leader paid a visit to the Enschede plant, he was given a demonstration of the AlisQI Quality Management System. His reaction was very positive.
“He was so enthusiastic! He said: ‘This is what we love: all data in one place … we should have this system in all our factories, we should roll it out worldwide’.
In his judgment, for a quality system, AlisQI is not expensive. He said: ‘This is just as it should be, I think it’s worth the price for what it delivers’ – of course, it was great to have him confirm what we knew already: that we had made the right choice with AlisQI.
This is what we love: all data in one place … we should have this system everywhere, we should have it worldwide.
Site Manager Diversey
Ruud Nijlant

The user-friendliness of AlisQI
As we saw earlier, the user-friendliness of the AlisQI platform was a factor in its selection for the Enschede plant. The system was rapidly implemented by a few key users.
“The rest of the staff finds it very easy to work with the platform. This is crucial for co-workers on the production floor, where we work in three shifts. Many people work the day shift and are not on the shop floor at night. But colleagues on the night shift can just continue with the information. AlisQI gives us seamless continuity.”
The interview with Nijlant draws to a close. He wants to mention one last thing. “We have noticed that if we want something new, which is not yet possible, AlisQI is very open to looking into it.
“Well, then we see if we can start building. For example, the OEE toolkit: you did not have one yet, but you can build it. So that was another success.
“In short, we receive a fast and very good service from the AlisQI team!”
We receive fast and very good service from the AlisQI team!
Site Manager Diversey
Ruud Nijlant

About Diversey
Diversey is a global market leader in industrial hygiene and cleaning solutions, and makes some of world’s best-known brands such as Persil, Cif and Vaseline. The company also supplies floor cleaning machines and a wide range of auxiliary services. Employing some 9,000 people worldwide, Diversey generated net sales of $2.6 billion in 2016.
The Diversey plant in the Netherlands is one of the company’s largest outside the United States, and manufactures liquid cleaning and disinfection products.
Let's plan a free demo!
We would love to show you how your factory can benefit from using our software, save up to 20% on time and reduce waste by up to 15%! Join our 1-hour online demo to get a clear impression of how AlisQI could help you work smarter.