Analyzing large amounts of data can feel like being surrounded by a dense forest. You know each tree is connected to others. But like the intertwined roots hidden underneath the forest floor, it can be hard to see all the connections.
That’s where control charts come in, giving you an easy and powerful way to visualize your data. SPC control charts enhance the understanding of your process and allow you to see where you’ve been and where you’ll be going, empowering more dynamic business and QC insights.
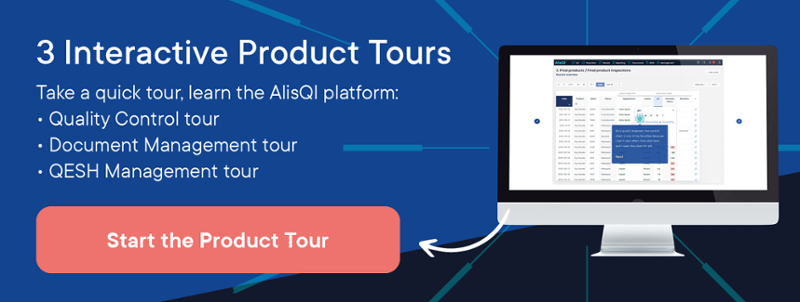
The core SPC charts
SPC charts have come a long way since Dr. Shewhart developed the first examples 100 years ago. Today, there are hundreds of charts available, each with its own list of pros and cons.
With all the options out there, it can seem nigh on impossible to select the right option. There is a core contingent of SPC charts, however, that can readily address most applications in the QC space. Working with these charts provides a more than solid starting point for exploring more advanced options:
- IX-MR chart
Plots the reading and what is known as the “moving range”, or the absolute difference between two consecutive data points.
Pros: Limited data needed for control limits, requires minimal calculations.
Cons: Cannot detect small changes in the process. - X-bar and R-chart
Two-component chart in which the X-bar plots the average or the mean of the process and how this changed over time, while the R-chart plots the difference between maximum and minimum individual values in each sample.
Pros: Distinguishes between variations in averages and standard deviations; widely used.
Cons: Requires additional charts for different characteristics on a single part. - Xbar-S (Standard Deviation)
Plots the average of the individual values and the standard deviation of the values.
Pros: Highly sensitive to mean fluctuations; signals process variations more accurately than the X-bar/R-chart combination.
Cons: Requires large sample sets.
What to consider in selecting an SPC chart
How to choose between this short list of SPC charts? Consider your sample size.
Sample size of 1
In certain scenarios, you are limited to a single data point. Think about cases in which sampling is expensive, time-consuming, or even destructive. In these scenarios, the IX-MR is your go-to chart to spot variability.
Smaller sample size (n >1 but < 10)
In complex production scenarios, you often produce only a handful of components each hour. In this situation, access to data is limited and getting a larger sample size is time and cost-prohibitive. When your sample sizes are smaller, the X-bar and R-chart is your strongest option.
Sample size greater than 10
When you are able to gather scads of data from automated devices or from high-speed production lines, your sample size is likely to be much higher. When data points are readily available, using an Xbar-S chart is the answer.
Automating the process
Working with SPC charts is no longer the complex, manual process it once was. Automated solutions can now streamline the input of data points, the parsing of that data and even the selection of the appropriate SPC chart.
Moreover, operators don’t need to keep an eye on control charts to ensure the stability of the process. A smart solution like AlisQI notifies them of any changes.
Watch this short video to learn about our SPC toolkit and contact us for an in-depth discussion tailored to your company’s needs.
